Benefits of an Efficient Reverse Logistics Process
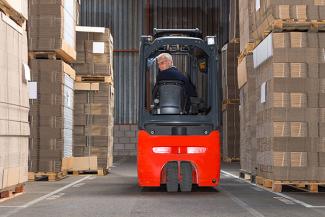
Optimizing your company’s reverse logistics system
What happens to your products after the point of sale? Are they easily returned if they’re faulty, recyclable if they’ve reached end-of-life, or able to be repaired? If the answer to these questions isn’t known, or the process to make those events happen isn’t well-defined, your reverse logistics system may not be operating at peak efficiency. Take a look at the benefits of an optimized approach, and get tips for improving your processes.
What is reverse logistics?
Reverse logistics is the process of moving products and materials at least one step back in the supply chain. It’s most often associated with returns and recalls, but it’s also used for recycling programs, asset recovery and disposal. Essentially, reverse logistics is how companies recoup value from returned goods or items that are no longer useful in their current state or location.
Examples of reverse logistics in action:
- Refurbishing damaged items so they can be resold
- Recycling parts or materials for new products
- Retrieving unsold merchandise from a retail store
- Returning pallets or other packaging to the manufacturer so they can be reused
Four benefits of reverse logistics
Because reverse logistics involves the same steps and processes as traditional “forward” logistics (customer service, transportation, inventory management, etc.), similar efficiencies can be found. By streamlining the way products move back through your supply chain, you can see benefits such as cost savings, happier customers and improved sustainability.
Decreased costs
There are several ways to cut costs with reverse logistics, from reducing transportation spend to reselling items that would have been a complete loss. Cost savings can be measured by tracking the total cost of ownership for each product type. If value is being regained from recycled and resold items, and the rest of the system is operating efficiently, profit margins will improve.
Increased customer satisfaction
The way your business handles returns could directly affect how customers feel about your brand. One survey showed it can even lead to company avoidance, with more than half of the respondents indicating that they would prefer not to buy from businesses with strict return policies. Both e-commerce and brick-and-mortar retailers can improve customer satisfaction with policies that:
- Provide a full refund
- Don’t require receipts
- Don’t require original packaging
Reduced waste
How many of your products are disposed of improperly? Reverse logistics can help you identify ways to reuse, resell or recycle materials that would otherwise end up in a landfill. This not only helps profit margins, but it also helps improve your brand’s reputation for social and environmental responsibility. To help promote waste-reduction initiatives to customers, many companies offer refurbishment incentives and recyclable packaging.
Less environmental impact
Eliminating unnecessary transportation is another way to boost sustainability efforts through reverse logistics. When building your supply chain, consider opportunities for consolidation and return avoidance. Options include:
- Having all returns shipped to central locations to reduce the number of long-haul shipments
- Establishing repair centers so items can be fixed locally or with less transportation
- Optimizing shipping schedules to bring products back to the manufacturing facility instead of deadheading
Read more about sustainable supply chains.
Utilizing reverse supply chain services
Damaged, surplus or unused goods require the same attention to detail as new materials, but managing them doesn’t have to be complicated. ArcBest® offers the logistics services you need to keep your supply chain running smoothly — no matter the direction.
For more information on how ArcBest can help you optimize your reverse supply chain, call 844-560-2532.